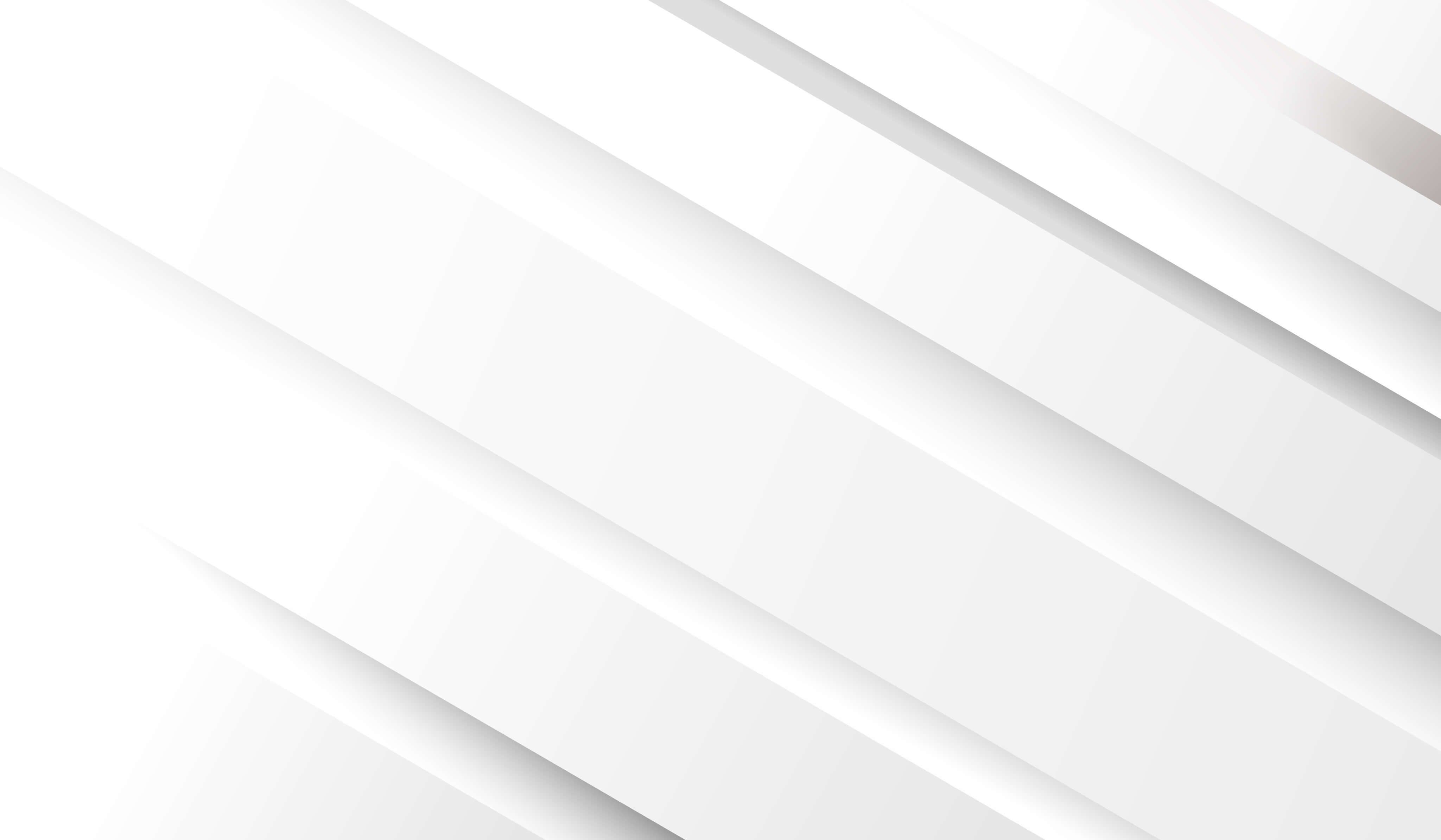
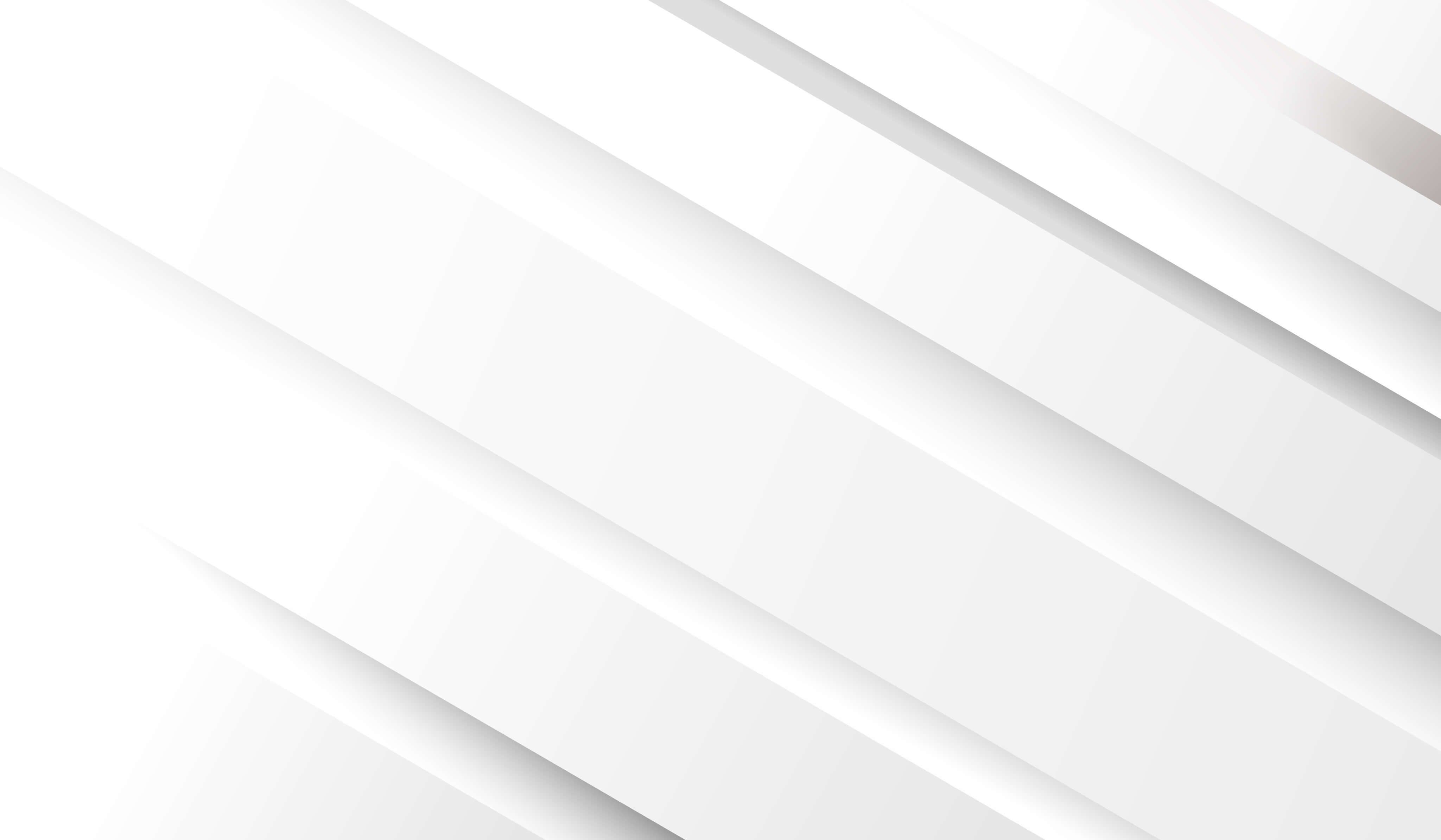
LABORATORY POLICY
We have always proceeded with the method of transparent inspection and review.
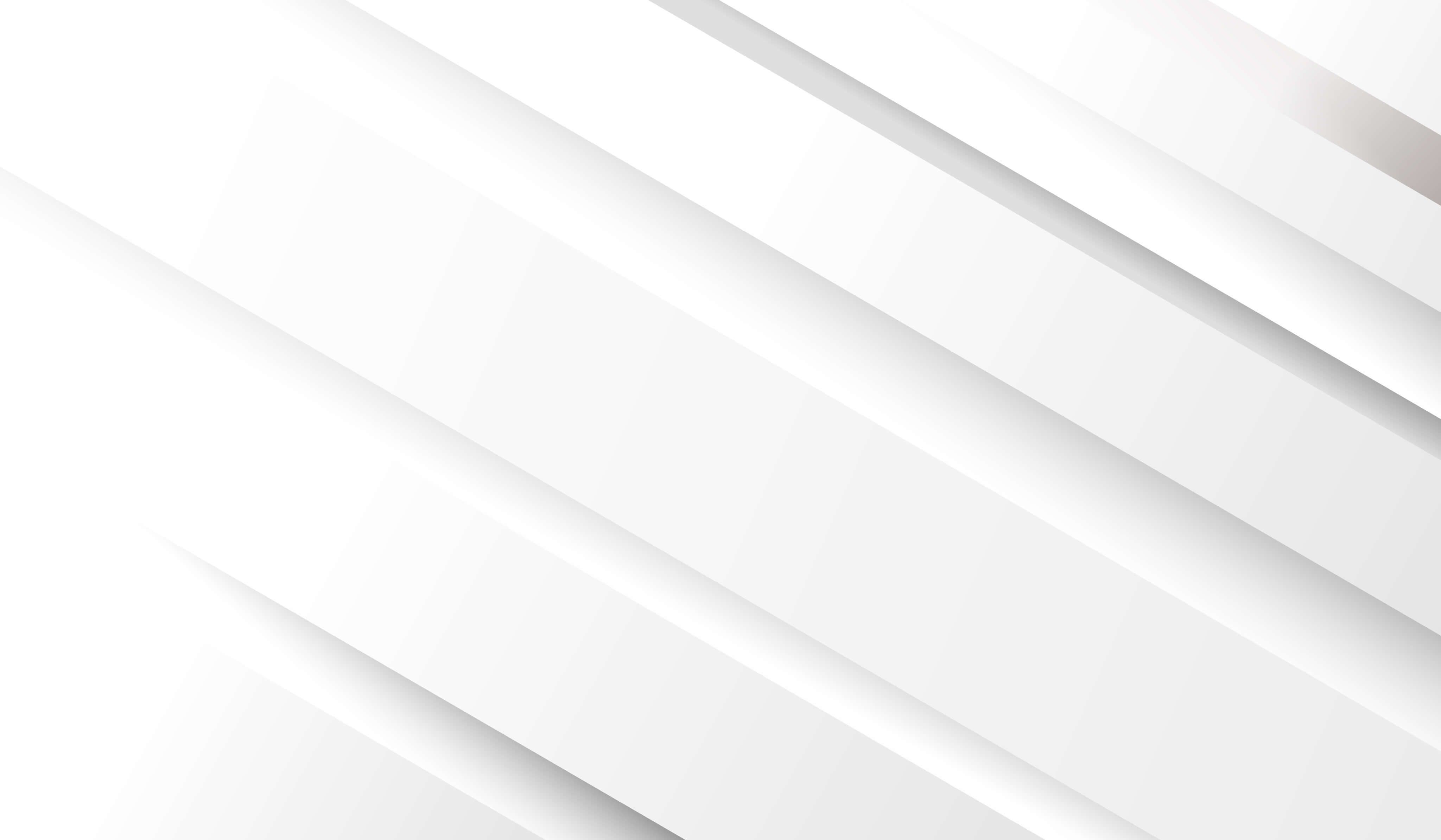
SERVICE AND CLAIM POLICY
INTRODUCTION
- YC INOX is dedicated to supplying customers with products in accordance with agreed to standards and specifications.
- YC INOX's early involvement in the development of customer requirements and communication of those requirements within the YC INOX organization is paramount to achieving customer satisfaction. [1]
- This general claims policy covers all products produced from YC INOX's facilities. It does not intend to cover all circumstances that may arise after.
- This general claims policy may be modified or superseded without notification.
- Only the most current version should be referenced when submitting a claim.
- The current version is available directly from the YC INOX Quality Assurance Department or website.
LIMITED WARRANTY
- YC INOX makes no other warranty whatever, express or implied. Any implied warranties of merchantability and all implied warranties of fitness for any particular purpose are disclaimed by YC INOX and excluded from this agreement.
- According to this claim policy, YC INOX's responsibility is limited to a 365-days period from the arrival date for international order and from the receipt of the material for domestic order.
- YC INOX warrants that products described or referred to on the face herein are of merchantable quality and conform in material respect to specifications accepted in writing by YC INOX.
- There are no warranties, express or implied, with respect to products sold hereunder which are misused, abused, or operated on mechanical equipment improperly designed or maintained or which are used, supplied for use or made available for use in any nuclear application of which YC INOX has not been notified in writing by Customer at the time of Customer’s offer for the products sold hereunder.
- For claims with merit, YC INOX will assume responsibility for the value of the material involved. YC INOX will not honor any unauthorized claims / costs.
- According to this claim policy YC INOX's responsibility is limited to such as being determined in the following sentence and the labor charges or any other direct or indirect charges shall be a matter of agreement between YC INOX and customer.
YC INOX RESPONSIBILITIES
- If material furnished by YC INOX does not meet an order's requirement, a claim should be submitted to the appropriate YC INOX representative.
- All claims will be evaluated on the basis of technical merit in line with published policies, industry standards, applicable specifications, contracts, and purchase orders.
- YC INOX reserves the right to replace, rework, sort, or issue credit for all nonconforming material at YC INOX’s option.
- Authorized disposition will be given after receipt of samples and subsequent investigation.
- After claim is reviewed and determination is made by YC INOX, a claim number will be issued or a denial of claim letter will be sent, if required.
CUSTOMER RESPONSIBILITIES
- The customer must notify YC INOX representative of the issue as soon as reasonably possible. [3] [4] [5] [6]
- In order to efficiently evaluate and process a claim, YC INOX retains the right to fully investigate the claim.
- This may include visits to the customers' site and processes that cause the claim.
DOCUMENTATION
Unless waived by YC INOX, a representative sample of the condition, digital photos with a size reference next to the condition, or a video are required for each claim.
All claims must be entered with the minimum of appropriate information (Claim Form).
All rejected material must be properly identified with your P.O. Number, the YC INOX’s Order number, invoice number, grade, dimensions, heat number and the original weight. The most efficient method is to attach a copy of the corresponding inspection certificate to the customer rejection object.
Evidence of the defect includes a representative sample of the defective material and a clear photograph of the defective product. The sample should clearly identify the condition of the product, as well as the heat number.
Where in the product the defect is occurring (ex. edge, middle, top, bottom).
When during the lifecycle of the product (at receipt, before or after processing) defect was noticed.
Full details of the claim reason must be provided. This must include a description of the defect, the weight or length of the product affected and the amount of product to be rejected.
SCRAP DISPOSAL
- No material can be scrapped without prior approval from YC INOX.
- Disposition of rejected products shall be in agreement between YC INOX and customer. [3] [4]
TRANSPORTATION, UNLOADING, RETURN POLICY
- For all shipments, customer is responsible for inspection and documentation of material condition during receipt and unloading. Any nonconformity must be noted on all paperwork received with the shipment.
- Claims for transit or handling damage will be accepted within seven (7) days of receipt of the material for international, and within two (2) days of receipt of the material for domestic.
- Full details of the damage and photographs (Including YC INOX packaging) of the material in the transportation or loading/unloading must be supplied with these claims.
- Customer is responsible for storage and protecting material from further deterioration while claim is under investigation.
- When it is necessary to return material to YC INOX, please contact with the appropriate YC INOX representative.
RAW MATERIAL NON–CONFORMANCE
- YC INOX will replace product or credit the cost on products which fail to meet customer's fabrication requirements due to raw material failure, and the material chemical or mechanical properties fall outside the requirements indicated on the customer purchase order.
- YC INOX is not responsible for the raw materials related to improper Customer's fabrication and processing, which leads to wrinkling, etc.
PRIME SURFACE
- Unless otherwise specified on the customer order, the top surface of plates, and sheets, or the outside surface of coiled products is considered the prime surface. [12]
RUST AND STAIN POLICY
YC INOX will evaluate all rust and stain claims to determine cause. YC INOX will not accept any claim for transit rust or stain related to improper storage or handling in a customer's facility.
According to this claim policy, YC INOX's responsibility is limited to rust which has corroded the surface of the material and leave pits or other surface condition nonconformance.
Claims are subject to review for proper transporting and storage.
Claims for rust on products where the customer has requested to limit or disallow the use of rust preventatives will not be honored.
Claims for rust on products that have already been fabricated by the customer or shipped to another location will be subject to investigation by YC INOX.
YC INOX will not be responsible for rust on products that have been subjected to processing or handling operations which disturb the rust preventive properties.
DIMENSION
- Requirements for dimensions will be according to customer specifications or purchase order accepted prior to production by YC INOX in writing, and/or consistent with applicable international specifications (ASTM, EN, JIS, etc.). [2]
- However, YC INOX will provide our product within customer specified tolerance if agreement to provide this product is acknowledged in writing prior to order acceptance by YC INOX.
SURFACE CONDITIONS(SHAPE) - GENERAL
- According to this claim policy, YC INOX's responsibility is limited to surface conditions that do not meet the requirements of the applicable international standard.
- When customer requirements demand a product that exceeds these standards, YC INOX must agree, in writing, to provide the material to the customer requirements.
- Where product does not meet either the international specifications (ASTM, JIS, EN, etc.) or the written undertaking of YC INOX. Claims for shape defects will be considered.
- Claims for surface condition defects are subject to review for damage during transportation or storage.
- Claims for surface condition defects that have already been fabricated by the customer or shipped to another location will be subject to investigation by YC INOX.
- YC INOX will not honor claims for visible defects found at an end user on material that has been processed and inspected at a downstream operation. These defects might include dimensions, roll marks, scale or other surface issues.
SURFACE CONDITIONS(SHAPE) - FLAT PRODUCTION
- Slight surface imperfections inherent in the rolling process are permitted. When products are delivered in coil form, the degree and extent of such imperfections may be expected to be greater due to the impartibility of removing short lengths of coil. [12]
- If a defect is visible at the beginning of a coil, please evaluate the status of the defect and check if the defect is continuous, please inspect up to 10% weight of the coil.
- If the defect diminishes at the point of 10% weight, please keep the evaluation process up to 5% weight more. If the defect is continuous, please set the whole coil aside including the used portion for YC INOX's further inspection.
- Shape claims should include evidence of the pre-processed coil. This evidence will be as received before leveling or slitting of the material.
- Claims will not be honored for the problems of coil O.D. and I.D. wraps.
- Cold rolled sheets should be free from imperfections such as roll marks, sliver, rolled in scale, scratch-gouge marks, pickle stain and seam defects. Flat products with No.1 finish or hot-roll anneal or hot-roll anneal and pickle finish is permitted to grind to remove surface imperfections within the thickness or width tolerance at any point not beyond the permissible variations in dimensions. [7]
- Repair of surface defects of plate by welding is permitted unless otherwise prohibited by other specifications or purchase order requirements. Defect depth shall not exceed 1⁄3 of the nominal thickness, and the total area shall not exceed 1 % of the plate surface area, unless otherwise prior approval from the customer is obtained. After repair welding, the welded area shall be ground smooth and blended uniformly to the surrounding surface. [8]
SURFACE CONDITIONS – LONG PRODUCTION
- Tubular products shall be uniform in quality and condition and have a finish conforming to the standard. Surface imperfections such as handling marks, straightening marks, light mandrel and die marks, shallow pits, and scale pattern will not be considered injurious or defects if the imperfections are removable within the tolerances specified for wall thickness. [9], [10], [11]
FLATNESS / EDGE WAVE
- YC INOX guarantees all sheet/plate product supplied will be within flatness tolerance as defined in international specifications (ASTM, JIS, EN, etc.).Flatness or edge wave is the maximum distance between the lower surface of the product and the flat horizontal surface, yet without any erect measurement.
- When customer requirements are more stringent than the aforementioned standard, YC INOX will provide the product as agreed in writing beforehand.
- When YC INOX provides a product that exhibits flatness/edge wave greater than either the agreed standard or international specifications (ASTM, JIS, EN, etc.), and the product is unsuitable for the designated end use, YC INOX will consider claims for flatness /edge wave.
THERMAL CUTTING DISTORTION
- YC INOX guarantees all sheet/plate product supplied will be within flatness tolerance as defined in international specifications or accepted in writing by YC INOX. Claims of thermal* cutting distortion will not be honored.
Distortion from laser processing is a result of the sudden rise in temperature of the material near the cutting zone - Distortion is also created by the rapid solidification of the cutting zone. In addition, distortion also can be attributed to the rapid solidification of material remaining on the sides of the cut.【14】
WELD INTEGRITY
- According to this claim policy for weld failure YC INOX’s responsibility is limited to material that fails in the weld seam area when tested as specified in the latest edition of the international specification.
- Claims for weld seam failures during customer processing are subject to review for appropriate fabrication practices, tooling and end cut condition.
MARKING
- Unless otherwise specified on the customer order, the method of marking and the material of marking for shipment shall be in accordance with the YC INOX’s procedures. Its quality shall be durable for at least one year in unheated and covered storage. Corrosion resistance of the product shall not be impaired by the marking. For flat products, one surface of the product shall be marked. This will normally be the prime surface of products, where only one surface is guaranteed to the required standard. As an alternative, for items that are wrapped, bundled or boxed, or where the surface is ground or polished, the marking may be applied to the packaging, or to a tag securely attached to it. [13]
SECONDARY PRODUCT
- Secondary product is sold without any warranty. The secondary product will be represented prior to sale with defects but this may not be all inclusive of the defects in the product.
REFERENCES
- [1] Section 8.2.1 Customer communication, ISO 9001, Quality management systems – Requirements
- [2] Section 1. Scope, ASTM A999/A999M, Standard Specification for General Requirements for Alloy and Stainless Steel Pipe& ASTM A1016/A1016M, Stan dard Specification for General Requirements for Ferritic Alloy Steel, Austenitic Alloy Steel, and Stainless Steel Tubes
- [3] Section 24. Rejection, ASTM A999/A999M, Standard Specification for General Requirements for Alloy and Stainless Steel Pipe
- [4] Section 30. Rejection, ASTM A1016/A1016M, Standard Specification for General Requirements for Ferritic Alloy Steel, Austenitic Alloy Steel, and Stain less Steel Tubes
- [5] Section 13. Rejection, ASTM A554 Standard Specification for Welded Stainless Steel Mechanical Tubing
- [6] Section 23. Rejection, ASTM A480/A480M Standard Specification for General Requirements for Flat-Rolled Stainless and Heat-Resisting Steel Plate, Sheet, and Strip
- [7] Section 10. Workmanship, Standard Specification for General Requirements for Flat-Rolled Stainless and Heat-Resisting Steel Plate, Sheet, and Strip
- [8] Section 21. Repair of Plate by Welding, Standard Specification for General Requirements for Flat-Rolled Stainless and Heat-Resisting Steel Plate, Sheet, and Strip
- [9] Section 28.13, ASTM A999/A999M, Standard Specification for General Requirements for Alloy and Stainless Steel Pipe
- [10] Section 33.1.13. ASTM A1016/A1016M, Standard Specification for General Requirements for Ferritic Alloy Steel, Austenitic Alloy Steel, and Stainless Steel Tubes
- [11] Section11. Workmanship, Finish, and Appearance, ASTM A554 Standard Specification for Welded Stainless Steel Mechanical Tubing
- [12] Section 6.6. Surface quality, EN 10088-2 Stainless steels - Part 2: Technical delivery conditions for sheet/plate and strip of corrosion resisting steels for general purposes
- [13] Section 8. Marking, EN 10088-2 Stainless steels - Part 2: Technical delivery conditions for sheet/plate and strip of corrosion resisting steels for general purposes
- [14] The challenges of laser cutting: Overcoming some common obstacles — THEFABRICATORR AUGUST 1998, MARCH 13, 2002, JIM WOLLENBERGER
- Version:2019-1
TECHNOLOGY EXCHANGE AND SHARE
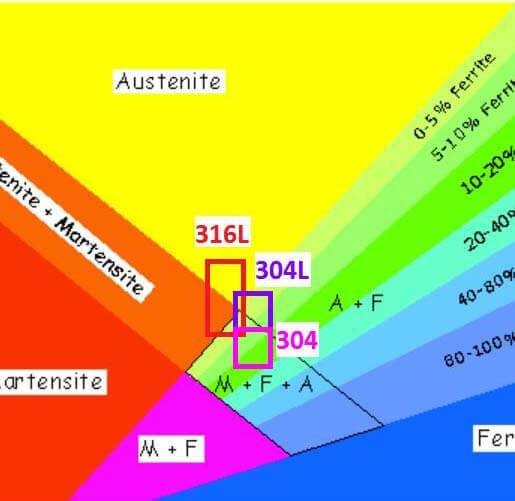
IS STAINLESS STEEL NOT MAGNETIC?
Usually we used as decorative tube or plate 300 series of austenitic stainless steel of material, they have magnetic...
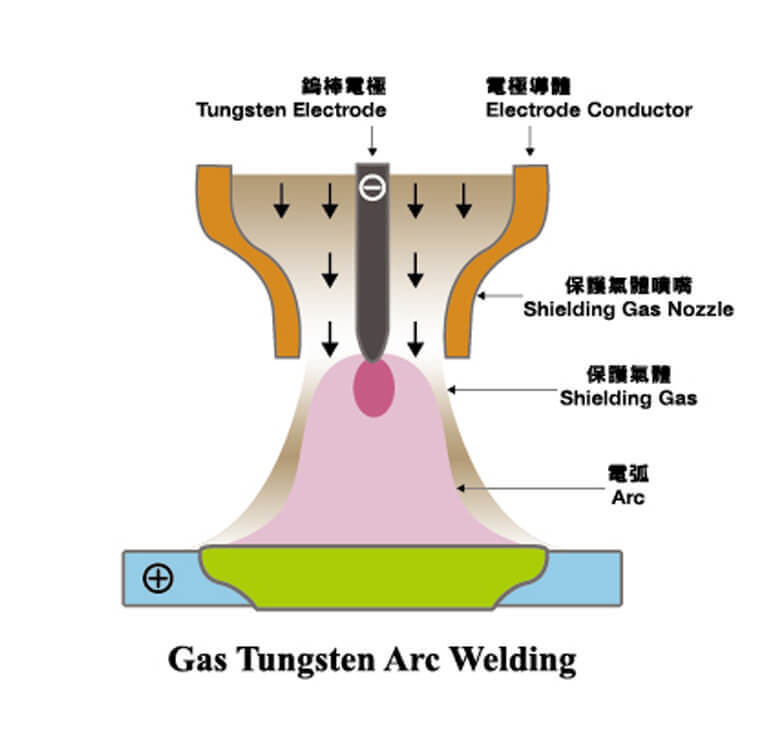
INTRODUCTION TO THE SOURCE PART A GTAW&PAW
Gas tungsten arc welding(GTAW) calls TIG(tungsten inert gas) a kind of arc welding。Using non-expendable tungsten electrodes...
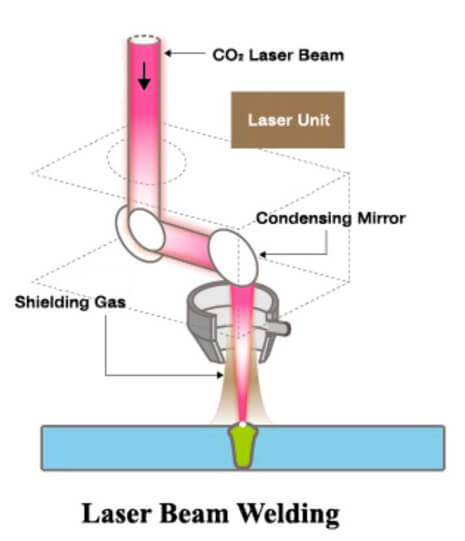
INTRODUCTION OF WELDING PART B LBW & SAW
Laser beam welding is a contactless welding method. There is no external force on the welded parts...
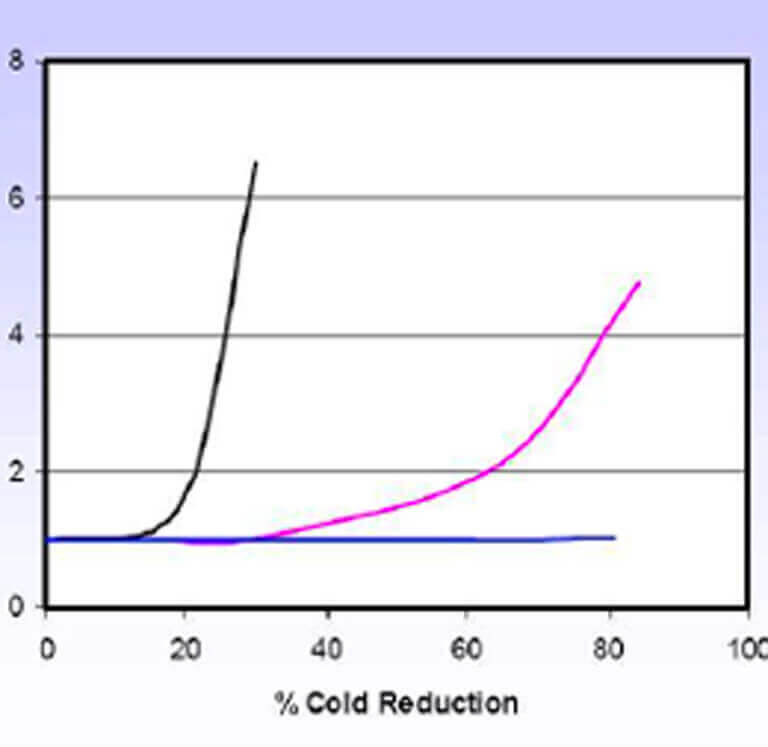
DISCUSSION ON MAGNETIC PROPERTIES OF COLD WORKING
In general, although the magnetic properties of the 300 series of stainless steel austenitic structure are not explicit...